The Herkules machine factory in Siegen, Germany, has been developing and manufacturing roll grinders for almost 100 years and is regarded as the worldwide market leader in this important supply segment for the steel industry. Since the year 2000, Herkules has been using Beckhoff control technology and automation components, which are programmed and implemented by its subsidiary HCC KPM Electronics for various types of plants and machinery.
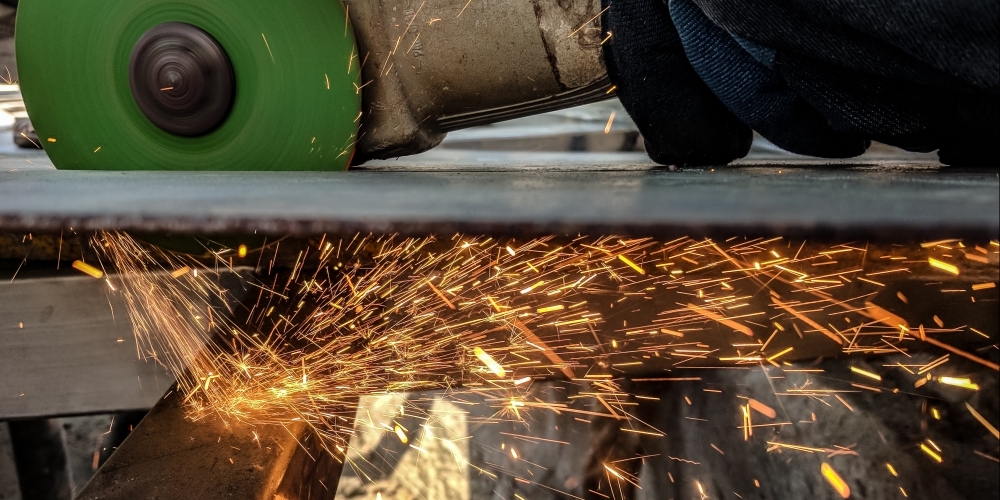
Herkules implemented a particularly demanding project with the delivery of a complete rolling workshop for the Chinese steel company Wuhan Iron and Steel (Group) Corporation (WISCO). The rolling workshop, also known as a roll shop, consists of a total of four roll grinders, two semiportal cranes for loading and unloading the roll grinders (loader) as well as the Roll Shop Management System (RSMS). In the rolling mill, sheet metal which has already been roughed down is rolled to the final thickness and quality. The end product is silicone steel or transformer sheet steel which is used for the manufacture of transformers and motors, for example.
Within a rolling mill, the roll shop provides the mainstay for the quality of the sheet metal to be rolled. Due to the extreme stresses on the rollers during the rolling process, the demands on a roll grinder are extraordinarily high with regard to grinding accuracy and uptime. These are among the most demanding tasks in the steel and smelting industry. The roll shop has to guarantee a work output of approx. 70 working and back-up rollers per day in a three-shift operation, with 97 percent availability.